Pre-Shipment Inspection
QCADVISOR helps importers, brands and e-commerce sellers guarantee defect-free deliveries by carrying out pre-shipment inspection (PSI) services right inside the supplier’s factory. A PSI is the last, independent verification that your goods are at least 80 % complete, correctly packed, and fully compliant with your quality specifications, industry standards and purchase order before the container doors close. Our inspection team, built on decades of QC experience in Asia, follows a proven six-step method that blends ISO 2859-1 (AQL) sampling with on-site functional, stretch, pull and fatigue tests. QCADVISOR’s digital platform lets you book, track and review every inspection report in real time, in six languages, at a price that keeps your supply chain agile.
- Early detection of critical, major and minor defects
- Quantity verification and carton integrity checks
- Independent third-party documentation for your customers and insurers
- Avoid costly rework, delays and customer complaints
By choosing QCADVISOR you turn the last mile of production into a moment of certainty—protecting brand reputation, margins and customer satisfaction across the world.
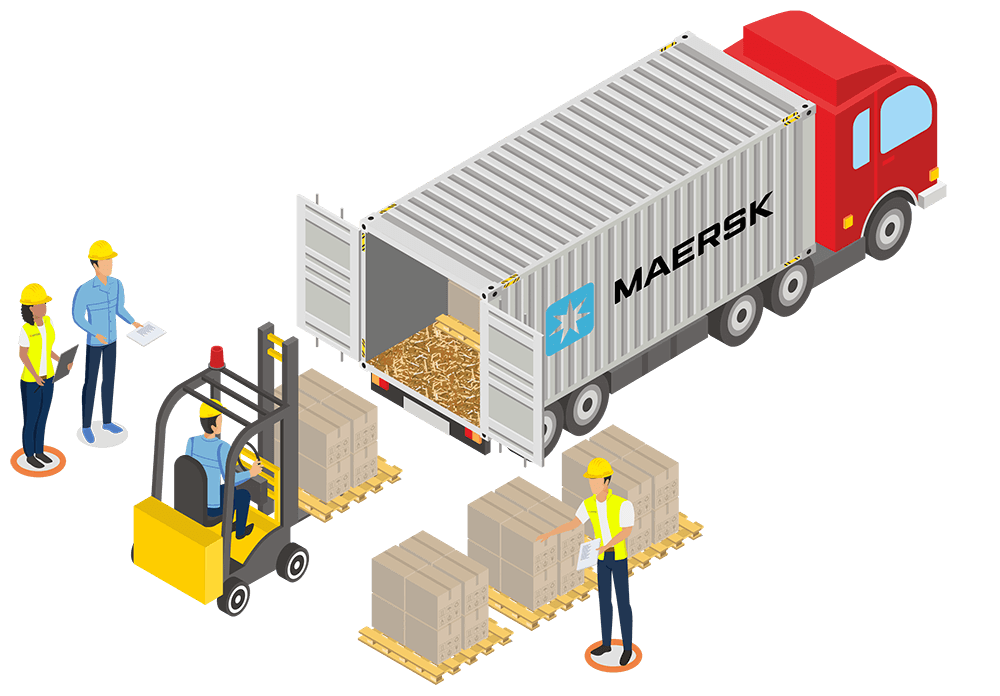
How Does QCADVISOR Perform a Pre-Shipment Inspection?
Our PSI experts arrive when production is ≥ 80 % finished and 100 % packed cartons are available. After an opening meeting with factory management, we pull a statistically valid sample size based on your order quantity and agreed AQL limits, then move through a rigorous checklist:
- Documentation review – purchase order, packing list, compliance certificates and labeling requirements.
- Quantity & assortment check – count finished goods, SKUs and spare parts against the PO.
- Workmanship inspection – cosmetic defects, assembly, sharp edges, loose threads, paint finish.
- Conformity verification – dimensions, weight, color, barcodes and logos measured against approved samples.
- On-site tests – stretch, pull, fatigue, drop, voltage, function or fit, mirroring your industry standards.
- Packaging & carton strength – ISTA drop test, sealing, humidity resistance, shipping marks.
- Container loading readiness – pallet pattern, moisture control, blocking and bracing methods.
- Final meeting – present preliminary findings, seal cartons if required and send photographs to you live.
Within hours you receive a rich inspection result summarizing defects, risk level and recommended action.
Why Work with QCADVISOR?
By combining razor-sharp quality control (QC) expertise with responsive service, QCADVISOR minimizes risk and maximizes customer satisfaction for every shipment.
- Specialised inspectors – Our industry-specific inspection team averages 5 + years on the factory floor, so they know the difference between a cosmetic blemish and a compliance breach.
- Data-driven reports – Clear pass/fail dashboards, high-resolution photos and defect trends allow quick, confident decisions from anywhere in the USA to Europe.
- Transparent pricing – One flat fee per factory visit, no hidden travel or weekend surcharges, keeping your landed cost predictable.
- Pro-active support – 95 % of clients recommend us because we don’t just flag problems—we coordinate corrective action with manufacturers and can arrange a free re-inspection when needed.
Partnering with QCADVISOR means fewer returns, tighter lead times, and the peace of mind that an independent third-party is protecting your brand at the critical moment of shipment.
When to Schedule Pre-Shipment Inspection with QCADVISOR?
Book a PSI once production is at least 80 % complete, packaging has begun and all value-added processes—such as labeling, bundling or manuals—are finished. It follows any pre-production qualification, production monitoring or during-production inspection (DUPRO) you may have ordered and comes immediately before container loading or a final random inspection (FRI). Scheduling 48–72 hours in advance lets our coordinators brief the factory, reserve the right inspector and guarantee the report reaches you before final payment or balance-of-order release.
What Is Included in the Pre-Shipment Inspection Report?
Our digital report is a comprehensive PDF and web dashboard, typically 30–50 pages, organised for fast executive review and deep technical reference:
- Summary page – overall result (Pass/NOK/Remarks), AQL tables, quantity verification and key photos.
- Defect catalog – critical, major and minor issues with zoomable images, part numbers and locations.
- Specification matrix – side-by-side comparison of measured data versus your quality requirements.
- On-site test results – detailed outcomes of pull, fatigue, stretch, rub, function or electrical safety tests.
- Packaging & carton section – ISTA drop photos, inner box checks, shipping mark compliance.
- Corrective-action advice – clear next steps, deadlines and re-inspection method if defects exceed limits.
- Inspector credentials & time-stamped images – traceability that satisfies auditors, retailers and insurers.
This documentation becomes an objective record that shields you from downstream disputes and reinforces your quality assurance program.
How to Schedule a Pre-Shipment Inspection with QCADVISOR?
- Create a project on our secure platform, upload PO, specifications and preferred inspection date.
- Receive quotation within hours; approve online to kick-start service preparation.
- Supplier confirmation – your factory confirms the date and arranges product availability.
- Inspection executed by the matched expert; real-time updates arrive in your dashboard.
- Report delivered typically within two hours of completion—letting you release balance payment, book freight and move forward with confidence.
Need help? Email us or reply to your booking confirmation; our multilingual coordinators respond within one business hour. Let QCADVISOR guard your next shipment and convert quality risk into competitive advantage.
Trusted Worldwide
We inspect products for the world-leading brands and marketplaces.
Join the league of successful brands who never compromise on Quality.
With QCADVISOR, embrace the advanced techniques that set market leaders apart. Are you ready to level up?